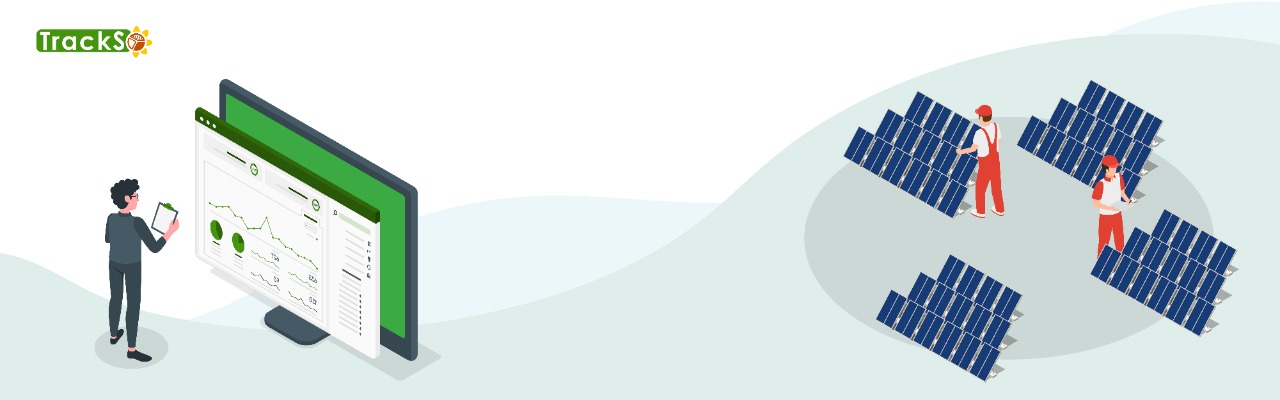
After covering Corrective maintenance last week, this week we will be going through Condition-based maintenance, it’s benefits and how remote monitoring helps in execution of it. This will be explained below in detail-
Condition-based maintenance is defined as carrying out maintenance following a forecast derived from the analysis and evaluation of the significant parameters of the degradation of the assets present on the solar PV site.
A prerequisite for a good Condition-based Maintenance is that the devices on-site can provide information about their state, in such a way that the O&M contractor can evaluate trends or events that signal a deterioration of the device. As a best practice, the device manufacturer should provide the complete list of status and error codes produced by the device together with the detailed description of their meaning and possible impact on the function of the device.
The asset Owner or interested party that wants to benefit from Condition-based Maintenance should, as a best practice, select “intelligent” equipment set with sufficient sensors, and opt for an appropriate monitoring software system which should be able to provide basic trending and comparison (timewise or between components and even between PV sites).
It is the exercise of using real-time information from dependable and efficient monitoring systems like TrackSo and agenda preventative measures such as cleaning or to head off corrective upkeep troubles by means of expecting disasters or catching them early. Condition-based upkeep influences when these measures occur, with the promise of decreasing the frequency of preventative measures and lowering the impacts and costs of corrective measures.
Condition-based Maintenance has several advantages, including –
- Optimising the safety management of equipment and systems during their entire lifetime;
- Anticipate maintenance activities (both corrective and preventive);
- Delay, eliminate and optimise some maintenance activities;
- Reduce time to repair and optimise maintenance and Spare Parts Management costs;
- Reduce spare parts replacement costs
- Increase availability, energy production and performance of equipment and systems;
- Reduce emergency and non-planned work;
- Improve predictability.